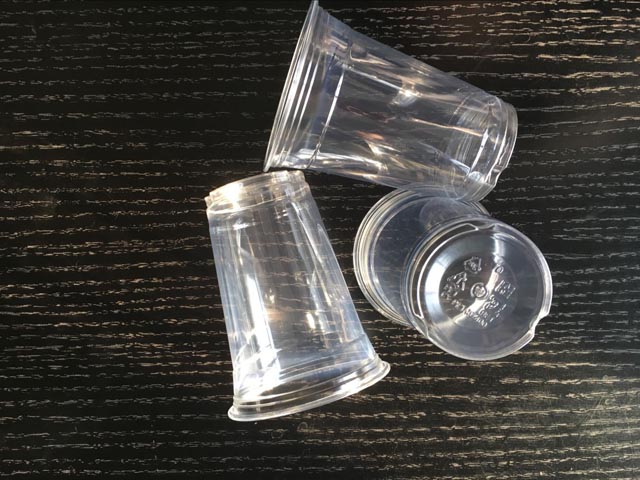
一、检测要求
-
外观缺陷检测
- 划痕检测:检测塑料杯表面是否存在划痕,划痕的长度、深度和宽度需进行量化评估,确定可接受的阈值范围。例如,划痕长度超过 5mm 或深度超过 0.1mm 判定为不合格。
- 污渍检测:识别杯子表面的污渍、油渍等杂质,根据污渍面积大小判断是否合格,如污渍面积占杯体表面积 1% 以上视为次品。
- 气泡检测:检查塑料杯壁内是否有气泡,对气泡的大小、数量及分布位置进行分析,单个气泡直径大于 3mm 或多个气泡聚集区域面积超过 10mm² 则不合格。
- 变形检测:判断杯子整体形状是否变形,如杯口圆度偏差超过 5% 或杯身弯曲度超过规定值则不符合要求。
-
尺寸测量
- 高度测量:精确测量塑料杯的高度,允许误差范围设定在 ±1mm。
- 口径测量:测量杯口的内径和外径,内径公差控制在 ±0.5mm,外径公差 ±1mm。
- 壁厚测量:检测杯子不同部位的壁厚,均匀性偏差不得超过 10%,且最小壁厚不得低于设计标准的 80%。
-
印刷质量检测
- 图案完整性:检查杯子表面印刷的图案是否完整,有无缺印、漏印现象,图案缺失面积超过 5% 为不合格。
- 颜色准确性:对比印刷颜色与标准色卡,色差值(如 ΔE)在规定范围内,例如 ΔE < 3 判定为颜色合格,超出范围则不合格。
- 文字清晰度:确保印刷文字清晰可辨,文字笔画模糊、断线或重影等影响阅读的情况视为次品。
-
装配完整性检测(如有配件)
- 例如检测带盖塑料杯,检查盖子与杯体的配合紧密程度,施加一定扭矩后,盖子不得松动或脱落,且密封性能良好,在规定压力下无泄漏现象。
二、检测方案
-
硬件系统
- 工业相机:选择高分辨率、高帧率的工业相机,如分辨率为 2000 万像素以上,帧率 30fps 以上的相机,以确保能够清晰捕捉塑料杯的细节特征。根据检测要求和塑料杯尺寸,确定相机的安装位置和角度,一般采用顶视和侧视相结合的方式,全面覆盖杯子的外观和尺寸信息。
- 镜头:搭配适合相机传感器尺寸和工作距离的镜头,如焦距 12 – 50mm 的变焦镜头,可根据不同的检测需求灵活调整焦距,保证成像清晰、无畸变。
- 光源系统:采用环形光源、背光源和条形光源组合的方式。环形光源用于照亮杯口和杯身表面,突出划痕、污渍等缺陷;背光源可用于检测杯子的轮廓和壁厚,通过透光性差异来判断壁厚是否均匀;条形光源辅助照亮杯子侧面,增强图案和文字的对比度,便于印刷质量检测。
- 机械传动系统:设计稳定可靠的传送带,确保塑料杯能够匀速、平稳地通过检测区域,传送速度可根据相机帧率和检测精度进行调整,一般控制在 20 – 50cm/s 之间。同时,配备定位装置,如机械挡块或传感器,使杯子在检测位置保持固定姿态,提高检测准确性。
-
软件系统
- 图像处理算法开发:
- 图像预处理:对采集到的图像进行灰度化、滤波等操作,去除噪声干扰,增强图像对比度,为后续特征提取和分析奠定基础。例如,采用中值滤波算法去除椒盐噪声,使用直方图均衡化方法增强图像整体对比度。
- 特征提取与分析:针对不同的检测项目开发相应的特征提取算法。对于外观缺陷检测,利用边缘检测算法(如 Canny 边缘检测)提取杯子的轮廓和表面纹理特征,通过分析纹理变化判断划痕、污渍等缺陷;对于尺寸测量,采用霍夫变换等算法检测杯子的圆形轮廓,进而计算直径、高度等尺寸参数;在印刷质量检测方面,运用模板匹配算法对比印刷图案与标准模板,结合颜色空间转换和色差计算方法评估颜色准确性。
- 缺陷判定与分类:根据预先设定的检测要求和阈值,对提取的特征进行分析和判定,将杯子分为合格、不合格两类,并对不合格产品进行详细的缺陷分类标注,如划痕缺陷、尺寸超差、印刷不良等,以便后续追溯和处理。
- 用户界面设计:开发友好的人机交互界面,操作人员可通过界面实时查看检测结果、统计数据、调整检测参数等。界面应显示清晰的图像预览窗口、检测结果列表、合格与不合格产品数量统计图表等信息,方便操作人员进行监控和管理。
- 图像处理算法开发:
-
系统集成与校准
- 将硬件系统和软件系统进行集成,确保各部件之间的通信正常、协同工作稳定。对整个检测系统进行校准,包括相机校准(如内参和外参校准)、光源亮度校准、尺寸测量校准等,保证检测结果的准确性和可靠性。在校准过程中,使用标准的塑料杯样件,对系统的各项检测指标进行反复测试和调整,直到达到规定的精度要求。
通过以上机器视觉检测方案,可以高效、准确地对一次性塑料杯进行全面检测,有效提高产品质量控制水平,降低人工检测成本和误差,满足大规模生产线上的检测需求。在实际应用中,可根据具体的生产环境和塑料杯特性对方案进行进一步优化和完善。